In the process of refining the design for my 3D printed glasses (yes, I'm still at it 🙂) and trying to streamline the lens ordering process a bit, because some folks have told me their optician, or their optician's lens supplier, didn't really want to mess with "unusual" things like this, I decided to draw and print a fake ophthalmic lens. You know, not optical-quality - or even see-through - but something that looks and feels like a lens, that can be mounted in my frames, to show an optician hands-on how it works and that it's not weird or delicate to work on.
I figured it would be a quick print in clear PLA, that would require only a bit of cleanup and mount right into the frames, complete with the bevel and the notch and everything. How wrong I was...
This part is almost impossible to print right:
-
It's modeled after a real bispherical lens with an offset optical axis. I mean it's optically incorrect, but it has everything a real lens would have: uneven edge thickness, one convex and one concave side.
You just can't set it flat on the bed in the slicer: none of it sits flat. The slicer has trouble generating support around the edge on the concave side that it interprets half of as overhang, and even if the beginning of the support doesn't get ripped off by the head and the print completes, the surfaces will be absolutely awful.
-
If you print it vertical - which frankly is the least bad option - then the bottom of the lens, under the support, will be a complete mess. The bevel won't even be visible. It takes quite some time to create supports that won't mess up the bottom of the lens too much
-
If you print it in clear PLA with only perimeters, it'll be transparent enough to see the spots were the perimeters are started at the next layer. And depending on your wall generation strategy, the spots where the printer tries to fill the voids will show up as round "halos" inside the lens.
The lens' thickness varies everywhere, so the slicer tries its best to fill each layer, but it's slightly different at every layer. At any rate, it reveals the slicer's idiosyncracies in tool path stragegy right away.
-
The bevel all around the lens is only 0.5mm high. If the printer is dialed in, the bevel will show as an actual 120-degree bevel near the front face of the lens, particular where the bevel is normal to the layer, about half-way up the lens if you print it vertically. If not, it will look like a barely-raised blob.
I've tried this print on 3 different printer and I just can't get a decent print. All I can do is play with the settings in the slicer until it comes out not too terrible.
So, that part is a bit frustrating for my original purpose, but it turns out to be a great part to test a printer and/or the slicer software! If you want to try it too, it's here:
https://github.com/Giraut/3D-printed_eyeglasses/raw/refs/heads/main/lens_example.3mf
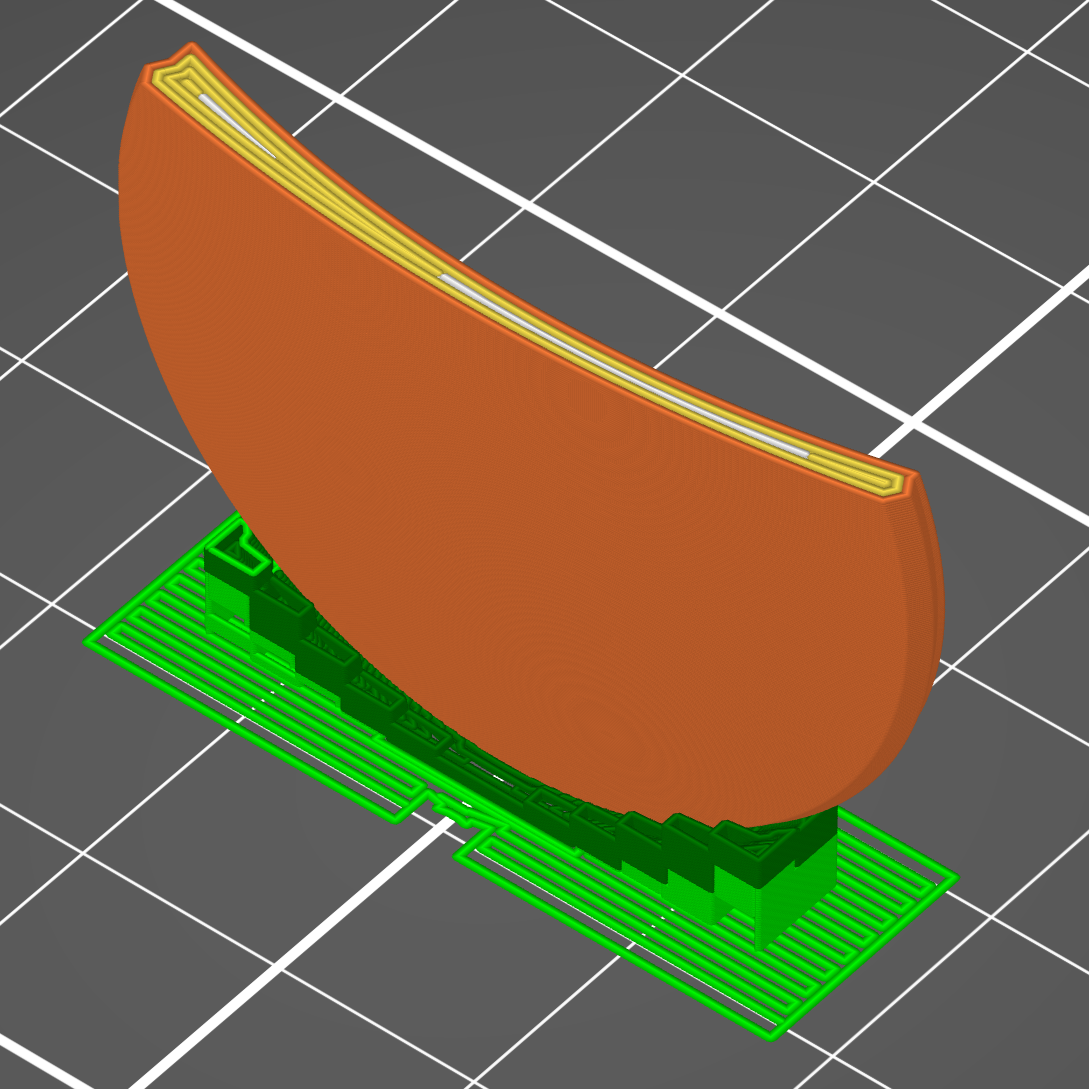
Sounds like the eventual end. Will be learning how to take raw circler optical lenses. As the optical centres do. And build the tools for folks to shape them at home.
Such a project would be a huge advantage to many 3rd world environments. And would likely be about embedding quality glass cutting blades etc into 3d printed frames/mechanisms. Likely from PA. With the ability to embed metal rods and gears where stability, strength is needed.
It's a guess ut I imagine the issue you have. Is most commercial opticians just see this as less option for them to sell overpriced frames. So agreeing to shape lenes for frames they dont sell. Is just a way to support the end of their profit line.
In the UK, when we started seeing the Chinese companies selling online glasses. We had lots of opticians refusing to give copies of the RX. Or limiting the positioning info they give. As all that part is NHS funded. Laws helped. But without legal force, companies ain't going to help themselves lose business if it is obvious.